Since 1947, the US Bureau of Labor Statistics (BLS) has been tracking Productivity across 307 different industries from 15 different sectors. One of those sectors is Manufacturing, which encompasses 133 different industries. The latest update shows a concerning trend.
On May 30th, 2024, the BLS published an update to their Annual Labor Productivity and Costs report, which quantified the productivity of each of these industries from 1987 to 2023. When focusing on the manufacturing sector and adjusting by the number of employees in each industry, productivity peaked in 2011 and has been in decline ever since.
Figure 1 shows the productivity per employee within the US manufacturing sector from 1987 through 2023, along with a trendline that forecasts a continued decline in 2024 and 2025.
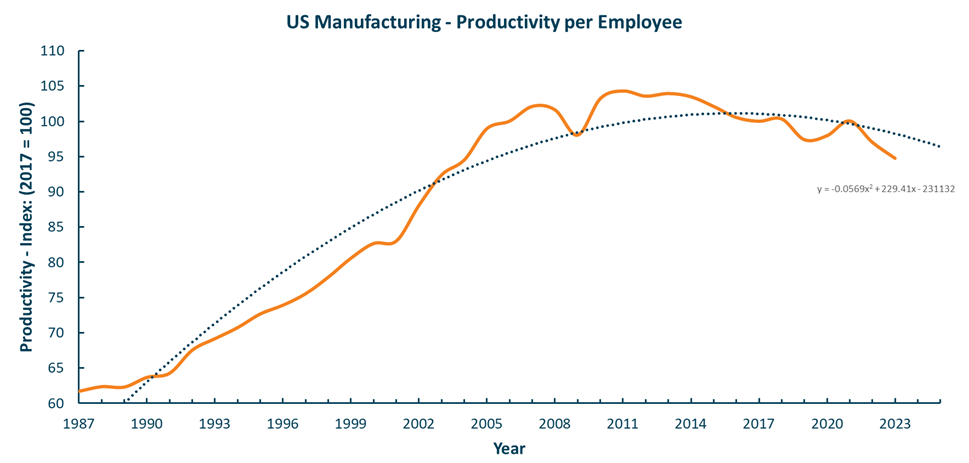
Productivity as defined by BLS: Productivity is a measure of economic performance that compares the amount of goods and services produced (output) with the amount of inputs used to produce those goods and services. https://www.bls.gov/k12/productivity-101/
What could be causing the decline in productivity? Have manufacturing employees been getting worse at their job since 2011?
Well, on average, yes. But let’s dive deeper.
The primary reason behind the declining effectiveness of manufacturing employees is the increased rate of Tribal Knowledge Churn. By 2030, all baby boomers will be older than 65. And by 2034, for the first time in US history, adults 65+ will outnumber children 18 and under. Older workers have accumulated the bulk of the experience and knowledge in the manufacturing sector, and they are now retiring in record numbers. They are passing these jobs along to a younger generation that have been taught computer skills, but not manual trade skills.
According to a study published by the Manufacturing Institute, 97% of surveyed companies are concerned about the Tribal Knowledge Churn of their workforce and the impact it will have on their future.
Since Jeff Bezos hasn’t succeeded (yet) in finding a way to allow humans to live forever, we are forced to find solutions to keep America competitive. Companies are taking steps to mitigate the churn of knowledge within their company by trying tactics such as: Increasing resources for onboarding, encouraging mentorships, offering training, and offering flexible work arrangements for 55+ employees.
However, the most effective way to retain and transfer knowledge is by leveraging technology. Implementing systems that capture and document workflows can bridge the gap between retiring employees and the new workforce, ensuring continuity and sustained productivity.
To address these challenges, companies should assess their workforce and identify potential knowledge gaps. Consider the following:
- How many employees are nearing retirement age within the next 5-10 years?
- Do we have a succession plan in place for critical roles?
- Are we leveraging the right technology to capture and disseminate knowledge?
- Is there a knowledge management system in place that employees use regularly?
- How would a sudden loss of key personnel affect our operations?
- How do we currently transfer knowledge from experienced employees to new hires?
By proactively addressing these questions and implementing knowledge retention strategies, companies can sustain productivity and thrive amidst demographic shifts.